Thermo-Elastics & STOP
Thermo-elastics and STOP are among the most challenging analyses to perform because they imply a chain of analyses using different mathematical models performed by different teams. Our approach, coming my from previous experience in some top international space missions, is an integrated approach as is also instructed in ESA's guidelines for Thermo-Elastic Verification, to which we contributed as part of ESA's T-E working group.
Core skills
Thermo-Elastic & STOP analysis and testing design for all mission phases according to ECSS and the TEV guidelines. We also use our uncertainty propagation method to analytically obtain the key drivers of the system, that can be thermal, structural or optical, from any part of the analysis chain.

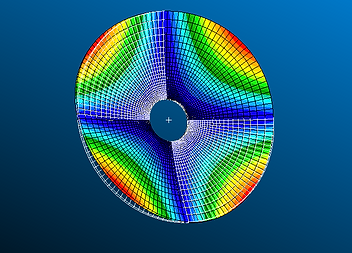
Thermal Analysis
Thermal analysis for thermo-elastics has important differences with regular thermal analysis. Just to name a few: the geometry should be aligned with the FEM, gradients are specially important and the selection of the worst thermal cases will probably not be the same as in regular thermal analyses. We build the thermal model from the beginning with this in mind.
Temperature Mapping
Transferring the temperatures from ESATAN to the NASTRAN FEM is a critical step. Typically the resolution of the thermal and the structural model are different and a physically consistent method is required to do this to preserve the thermal gradients. We use the PAT (Prescribed Average Temperature) method implemented in ESA's tool PySINAS.
Structural Analysis
This is the last step of the thermo-elastic analysis. The temperature field yields fields of stress and deformation, which we have to validate against structural and performance requirements. As for the thermal model, the structural FEM needs to be tailored to perform TE analysis. The elements involved in the thermo-elastic deformation mechanisms, such as telescope mounts or sandwich panels, are modelled taking this into account.
Optical Performance
In the case of optical systems, one more step can be added to this chain, and it is using the structural displacement outputs to evaluate the effect in the performance of the optics. At this time we are involved in an ESA project to evaluate the interface between the structural analysis and the optics, using ZEMAX and SigFit. Gravity release, jitter, as well as the optics assemby procedure can be introduced as well in this analysis, as we code them into Zemax using the API.
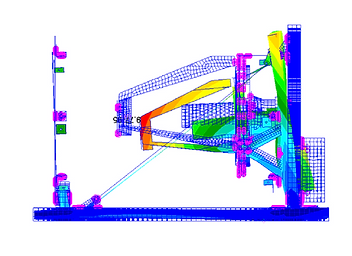
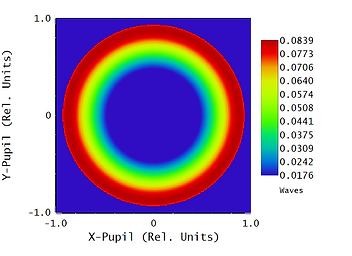